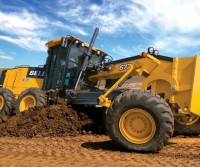
GPS Technology On The Rise In Construction
People are getting used to that soft, female robotic voice in their cars telling them where to make the next left turn as they pass through an unfamiliar city’s traffic tangle. But they might not imagine that the very same GPS technology is sitting on the control panel of the heavy equipment at the nearby highway construction site. Like, can’t dozer drivers find their work sites by themselves? Actually, using satellite technology to pinpoint the position of a backhoe’s shovel or direct the blades of a bulldozer or grader is not all that new.
In fact, since GPS signals can tell you where you are within a foot or so, it has largely replaced the surveyor’s string and chalk as the method of choice to tell you what spot to dig in and how to coordinate the precise locations involved in most construction sites.
A small screen in the cab of a dozer, for instance, can tell the operator within inches, exactly where he is on the site. It can tell him how steep the grade of a road should be and if he’s doing it properly as the job goes along in real time, without consulting a foreman.
For a farmer, the technology can guide tractors and combines, helping adjust the rate of planting and monitoring crop yields.
Big-dig construction equipment companies are on to all of this, and one in particular – NMC of North Platte, NB – is making it a specialty. The third-generation business with more than 600 employees has a whole division dedicated to it – NMC Technologies – with a dozen dedicated specialists developing and selling the precision-digging high-tech hardware.
Small Change Yields Big Results
Sometimes small changes can make a big difference in the productivity of your machines. For example, a recent “minor” development in some grade control systems eliminates the need for dozer operators to stop production in order to tune the automatic blade control performance. Sounds like a small thing, but good operators want to “hit it and get it” when they get on-site and start pushing dirt.
With almost all grade control systems, operators have to test and tune for how the dozer responds to the type of material they are grading by making a “test” pass… and then make the pass again once they get tuned in. Plus, in many cases they need to stop the machine and re-calibrate the valves when the materials they are grading change… like going from gravel to topsoil.
Today, manufacturers are working on improvements to grade control that reduce or eliminate the need to make a “test” pass. Trimble’s system uses a feature called GradeMax, that has improved algorithms to increase the dozer performance without the cost of additional inertial sensors. Optimizing the valve and blade controls enhances real-time control and accuracy, reducing the need for the “test” pass. Plus, the data update rates are doubled… which increases smoothness for all the grading tasks. The higher update rates and better valve control allow the operator to grade a faster, more consistent run with tighter accuracy.
So, basically, the operator can just start working, and follow input on the controller to fine tune while pushing dirt. Just drop the blade, hit the automatic blade control and fly… for a much more productive result!
Talk to your technology dealer to see if they have a similar feature available. Like I said, it’s a small change, but a big improvement.
Courtesy of Construction Equipment Blog
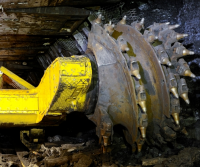
Maintenance Made Simple
Heavy machinery requires constant maintenance to keep it in good working order. Conversely, poorly maintained large machinery equipment runs inefficiently. Breakdowns are costly and safety is also an important consideration.
1. Stay on top of large machinery operator training
Many types of large machinery have multiple operators. One of the ongoing inspections on any checklist should be overseeing the correct operation of the equipment.
Large machinery should be inspected as soon as it is purchased. Operator training is usually done at that point, but training needs to be kept up. Employees come and go, skills become rusty and poor operation leads to breakdowns.
Operator manuals can be revised for the specific work situation. They can be rewritten in simpler language. A short manual can be provided to each operator for easy reference. And, if you operate in a paperless environment, you can rest assured operators use the most current version of each manual.
One other note is to identify best practices, which can then be applied to other facilities or geographic locations. The knowledge you learn about how to maintain your equipment can become quite valuable – be sure to best leverage this important knowledge and use it at every applicable location.
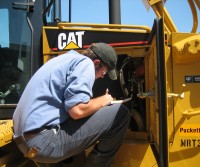
Secrets Of The Trade
To reduce repair costs and minimize losses in productivity, more manufacturing operations are turning from preventive maintenance (maintenance based on a fixed schedule) to proactive maintenance and predictive maintenance (maintenance based on objectively determined need) in order to protect their high-value assets. Condition monitoring of crankcase, hydraulic, motor bearings and gear lubricants plays an important role in the maintenance of equipment including heavy machinery and plant equipment.
Currently, lubrication condition monitoring is typically accomplished by taking samples in a prescribed manner and sending the samples to a laboratory for analysis by an array of analytical technologies.
The recent availability of field-portable, rugged and easy-to-use analytical instruments for use directly at the site of manufacturing operations changes how the condition of in-service lubricants can be monitored. These field-ready analytical tools provide users with near real-time information and allow them to monitor the lube point level of machinery quicker and easier than traditional methods where samples are sent to laboratories for analysis. This results in rapid, actionable decisions, thus enhancing proactive maintenance programs.